Single-screw extruders have carved a unique niche within the vast world of manufacturing machinery. Over the decades, their role in the plastics industry has evolved, bridging the gap between raw materials and finished products that touch every aspect of our lives.
What Are Single Screw Extruders?
Simply put, a single-screw extruder is an innovative piece of equipment with a single rotating screw encapsulated within a cylindrical barrel. The rotation is integral to its function — it’s responsible for melting, mixing, and pumping material, predominantly plastic.
As this screw rotates, frictional heat is generated. When synchronized with external heaters embedded in the barrel, it ensures that the raw material is seamlessly melted and then propelled through a shaping die, creating the desired form or structure.
Historical Overview
Historically, the inception of single-screw extruders marked a turning point in the manufacturing landscape. Before their introduction, the processing and shaping of materials, especially plastics, were labor-intensive and less precise. The advent of these machines streamlined production processes, delivering increased efficiency, consistency, and scalability.
The Unwavering Significance in Today’s Manufacturing
Fast forward to today, single screw extruders are not just machinery; they’re the backbone of countless production lines across the globe. These extruders play a pivotal role, from basic utilities like pipes and films to intricate products such as medical tubing, wires, and custom profiles.
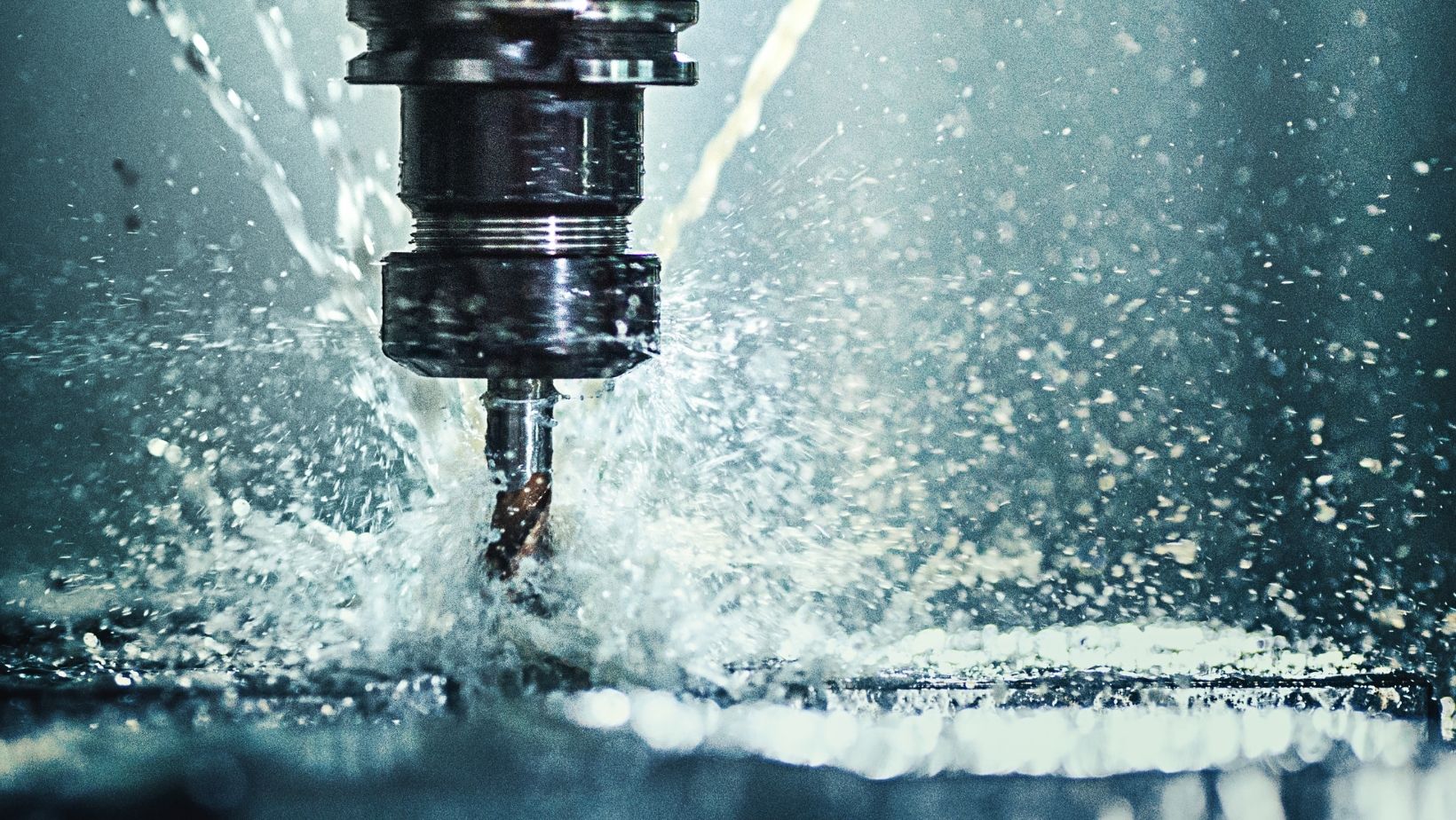
One of their standout features is maintaining a steady and consistent material flow. This continuous process ensures that the final output remains uniform and of the highest quality. Furthermore, the extruders’ adaptability is commendable. Modern iterations allow operators to tweak many parameters, ranging from temperature and screw speed to barrel pressure, ensuring optimal processing for diverse materials.
Technological Innovations and Advancements
As with any machine central to industrial processes, single-screw extruders have witnessed numerous technological enhancements. Current industry trends focus on energy efficiency, maximizing output rates, refining melt quality, and ensuring seamless adaptability to a spectrum of materials.
A notable aspect of these extruders is the design of the screw. Given the diversity of materials available today, manufacturers constantly innovate screw designs to cater to a broader range of inputs. This ensures uniform melting, intensive mixing, and a better end product.
Add to this the modern control systems, and you have a machine that provides unparalleled control over every facet of the extrusion process, ensuring that the end products consistently meet stringent quality standards.
Embracing Sustainability
In the current global climate, where sustainability is no longer a choice but a necessity, the machinery used in manufacturing plays a critical role in shaping environmental outcomes. Single screw extruders, due to their pivotal role in plastic processing, have been central to industry-wide recycling efforts.
Modern-day extruders have been innovatively designed to process recycled materials with the same efficiency as virgin materials. This pivot towards embracing recycled inputs underscores the industry’s commitment to ecological sustainability.
Bausano stands out as a beacon of innovation and commitment within this sphere. With their extensive range, including the single screw extruders, https://www.bausano.com/en/extruders-range/single-screw-extruders encapsulates the ethos of modern manufacturing — efficiency intertwined with environmental consciousness.
In Reflection
Summing it up, single-screw extruders, though often overshadowed by the final products they help create, are the unsung heroes of modern manufacturing. As the world of production grows ever more complex, these machines are a testament to human ingenuity, innovation, and our relentless drive to improve.
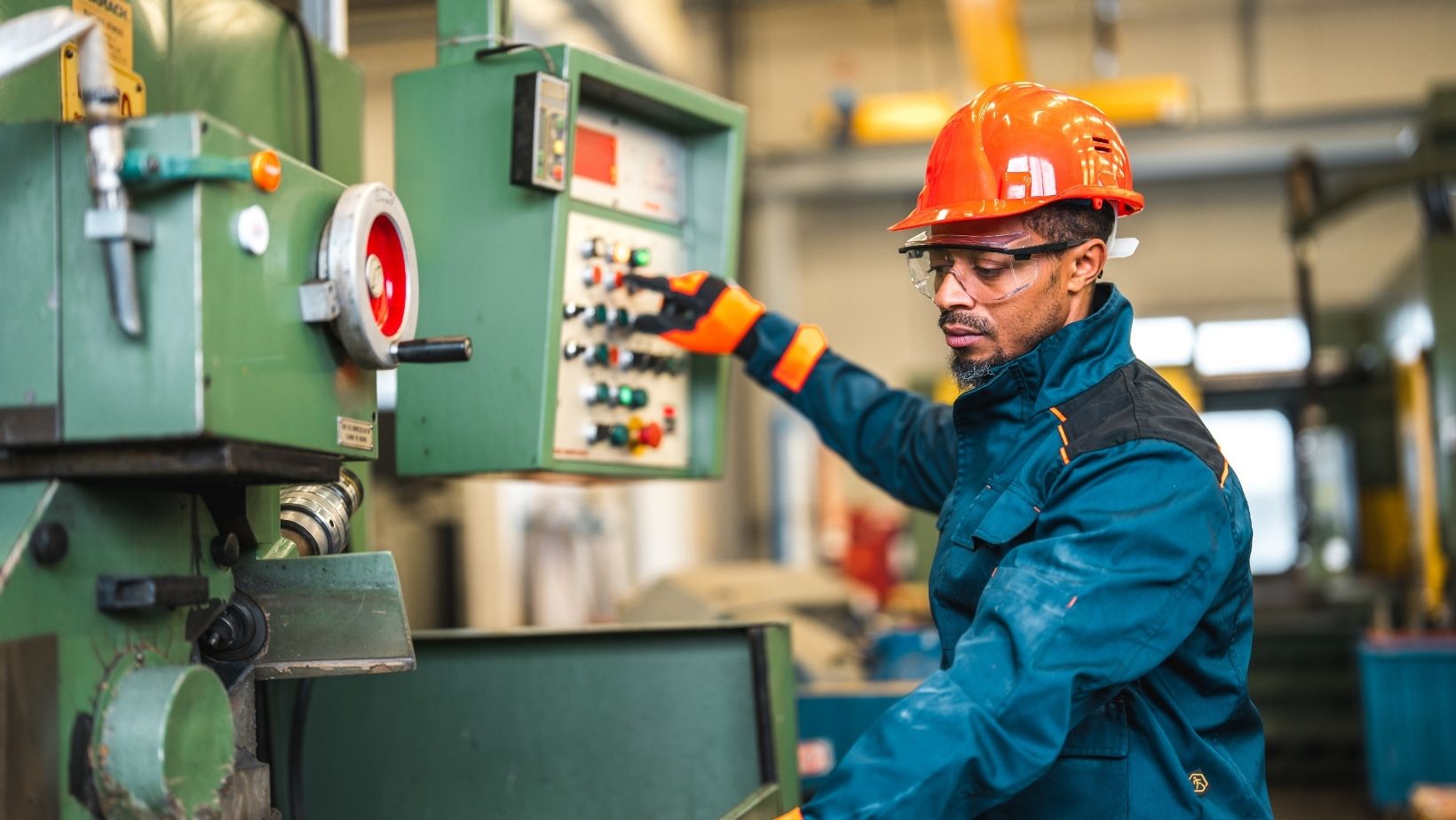
Companies like Bausano further amplify this by continuously pushing the boundaries of what’s possible, ensuring that as we stride into the future, we do so with machines and methodologies that are efficient and harmonious with our planet.