As an experienced financial analyst, I’ve spent years unraveling the complexities of cost accounting. One concept that’s crucial to understand is the total product cost per unit under absorption costing. This method, which includes all manufacturing costs — both variable and fixed — in the unit product cost, can significantly impact a company’s financial reporting and decision-making process.
Absorption costing, also known as full costing, is a common approach used by businesses to determine their total product cost per unit. It’s an essential tool for managers to accurately calculate profitability, make informed pricing decisions, and evaluate inventory levels. However, it’s not without its nuances and challenges.
The Total Product Cost Per Unit Under Absorption Costing is
Let’s dive in-depth into how we calculate the total product cost per unit under absorption costing. It’s critical to understand this to make effective business decisions. Below there’s a walkthrough of this calculation:
- Identify Direct Costs: Start by identifying all direct costs associated with the production of your product. It’s no secret – these elements form a significant part of your total product cost.
- Determine Overhead Costs: Factor in overhead costs, which include elements like rent and utilities that may not directly correspond to production. These costs are distributed across all units produced, impacting the total cost per unit.
- Calculate Total Product Cost: Add up the direct costs and allocated overhead costs to find the total product cost. This figure gives you a comprehensive view of the cost tied to each unit of your product.
By now, you’re likely seeing the value in absorption costing: it provides a complete picture of your product costs which aids in crafting sustainable pricing strategies.
It’s worth noting though that it has potential downsides too: its complexity and the possibility of inflating profit levels. There’s some potential for businesses to overallocate overhead costs, which could make products seem more profitable than they really are.
Definition
In this section, we’ll delve into the nitty-gritty of absorption costing. We’re setting the stage to help you better understand what this concept means and how you can calculate the total product cost per unit.
Understanding Absorption Costing
Absorption costing, also known as full costing, is a method used in the accounting world to capture all costs associated with production. The approach is direct and thorough because it absorbs or includes both the direct and indirect costs related to the product.
When we talk about direct costs, we’re referring to the cost of raw materials and direct labor used in a product’s production. On the other hand, indirect costs cover a wider scope—this could include utility, equipment depreciation, and even the salary of the plant manager.
It’s essential to understand that under the absorption costing method, fixed overhead costs are spread over all units produced during a period. This method provides a more accurate product cost per unit helping business owners and executives in making informed financial decisions.
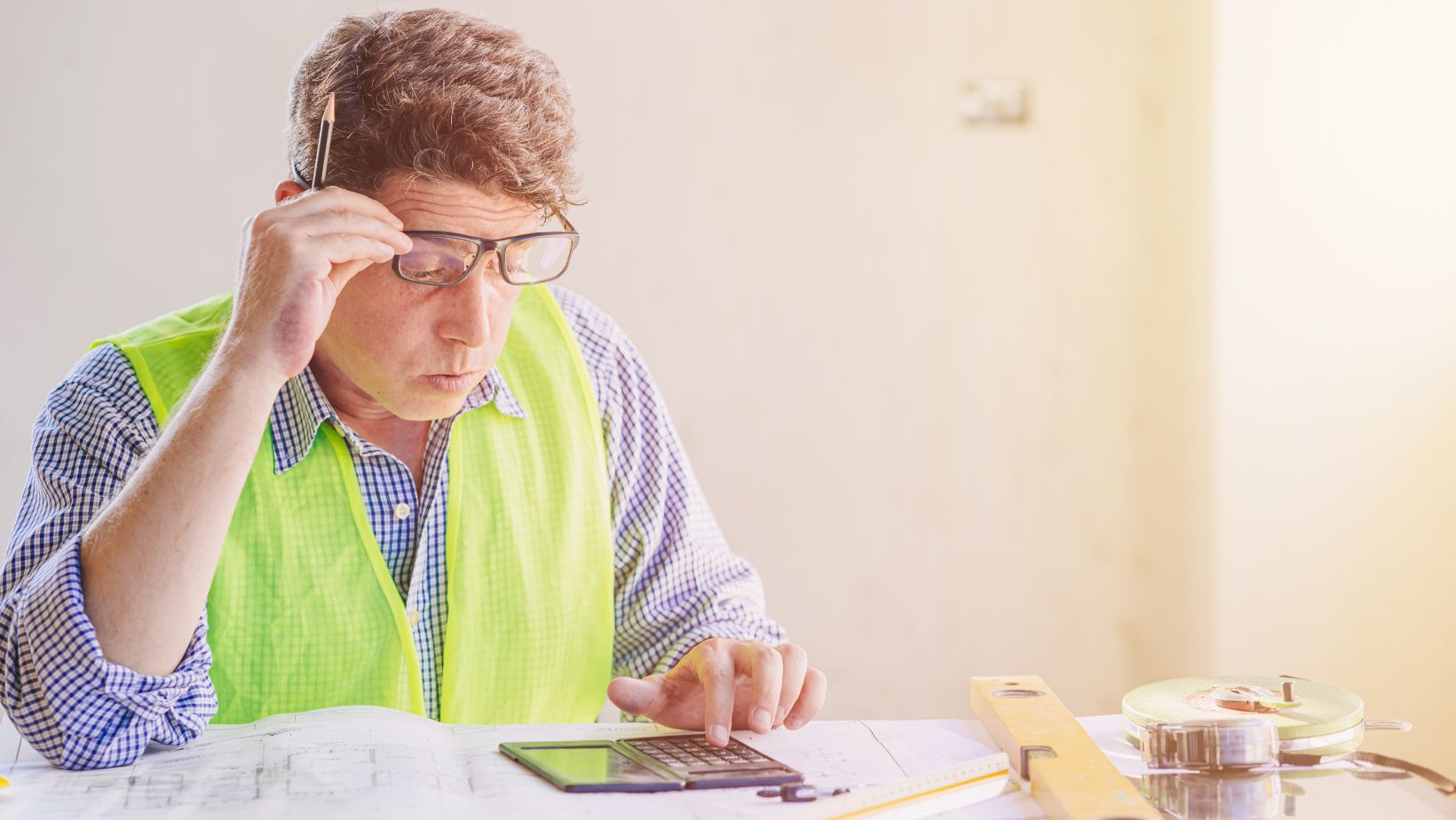
Components of Total Product Cost
With a firm grasp on absorption costing, we can delve into the intricacies of the total product cost per unit. Through this, you’ll attain a deeper understanding of your company’s cost structure and be equipped to make better financial decisions for your business.
Direct Materials Cost
The calculation begins with the Direct Materials Cost. This encompasses the expenses incurred in purchasing the raw materials specifically used for the manufacture of the product. When calculating, remember that any waste or excess material also factors into the cost. Persona experience tells me, accurate tracking and forecasting of raw materials are pivotal to reduce wastage and effectively control the cost.
Direct Labor Cost
Next component is the Direct Labor Cost – the wages paid to the employees directly involved in the creation of the product. Again, it’s critical not to overlook any aspect of labor cost, which can include salaries, wages, bonuses, and payroll taxes. To illustrate, if an employee spends 2 hours on a single product and they earn $15 per hour, their labor cost would factor as $30 into the cost of the product.
Conclusion
Absorption costing gives us a complete picture of product cost per unit. It’s not just about raw materials or direct labor—it’s also about manufacturing overhead. By taking into account all these components, we get a more accurate cost per unit. This method can be a game-changer in decision-making. It helps us understand the true cost of producing a product, which can influence pricing, budgeting, and even product development decisions. So, if you’re not already using absorption costing, it’s time to consider it. Remember, understanding your costs is the first step to maximizing profitability.