Production Line Balance Optimization can be a difficult process. It requires creating a simulation model that considers including supply levels and customer demand. The good news is that your simulation model has been developed; it’s easy to use to see whether your production lines need adjusting.
In this blog post,, I’ll explain the V-curve and how production line balance optimization works by using it as an example of how optimizing your factory layout can help you save time and money!
What is the V-Curve?
The V-Curve is a graphical representation of the relationship between inventory levels and throughput. It shows that as you increase inventory, your throughput decreases. The shape of the curve resembles a “V” because it starts at high volumes and then drops off as you increase your inventory levels.
In general terms, an increase in demand will increase lead time if no change has been made to capacity or other resources such as human capital (e.g., workers). In this case, we would say that there has been no change in efficiency since they are still working at 100% utilization rates, but overall effectiveness has decreased due to increased lead times caused by higher order quantities (OQs).
The V-curve shows the relationship between supply, demand, and inventory levels.
The V-curve visually represents the relationship between supply, demand, and inventory levels. It shows how much inventory is required at each point in time to ensure that customer demand can be met with minimum cost.
The V-curve can determine whether you have enough or too much inventory for your production line balance optimization strategy.
The concept of the V-Curve
The V-curve shows the relationship between supply, demand, and inventory levels. This shape of the curve affects inventory levels, costs, and customer service. For example, if you have a positive slope (the line slopes up), then your inventory will increase over time as you produce more products than customers need or want to buy at any given point in time.
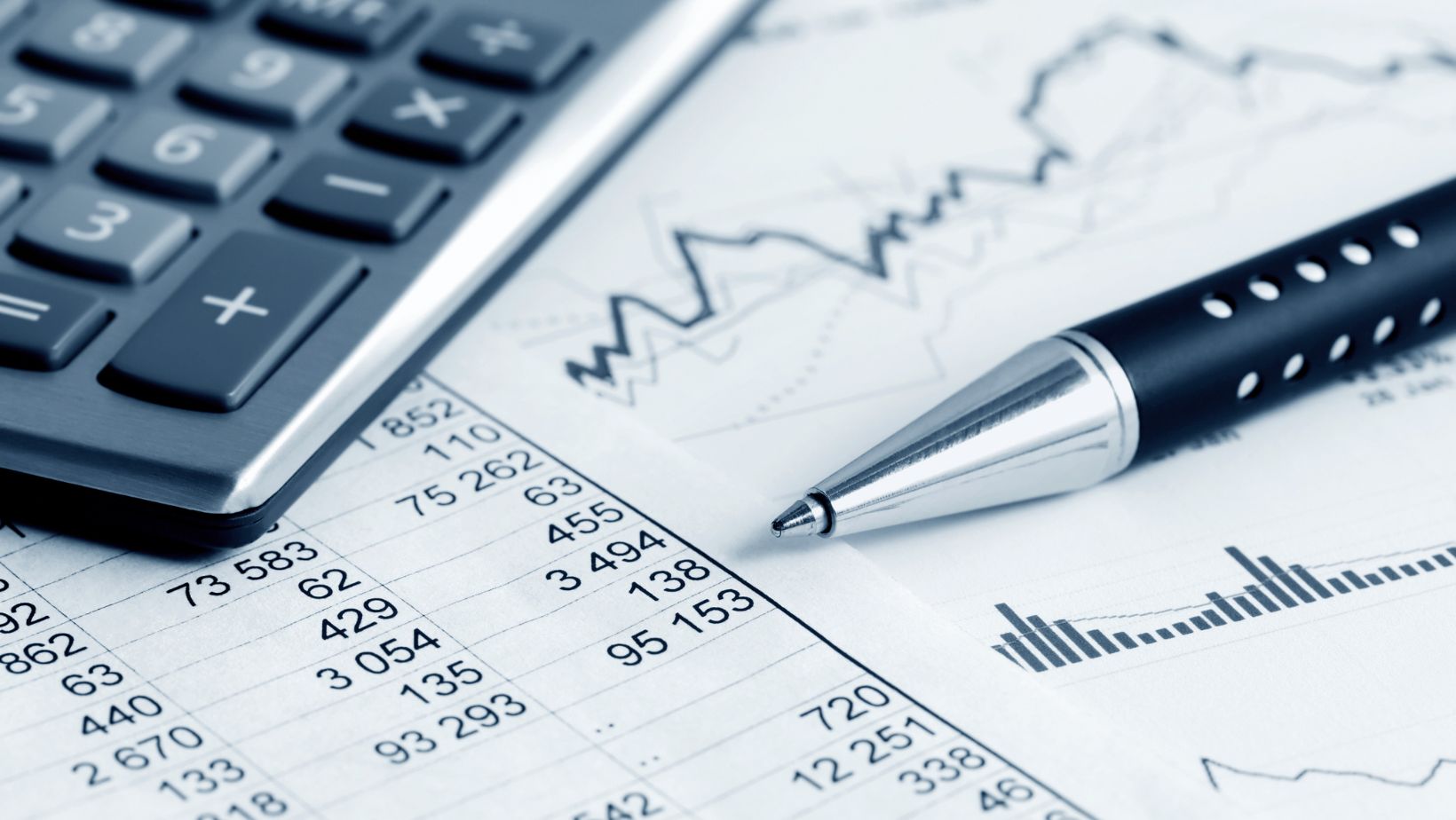
A negative slope would mean that your output rate is higher than demand, which allows you to reduce costs by reducing stock levels while still meeting customer orders on time.
The key objective of production line balance optimization
The key objective of production line balance optimization is to try to get your V curve’s shape as close as possible to a 45 degree angle. A V curve with a slope closer to 45 degrees means that more units are produced per hour, which results in higher throughput and lower costs.
The closer your V-curve is to a 90-degree angle (vertical), the more off-balanced your production line will be.
What are the 4 steps in Production Line Balance Optimization?
The first step in optimizing production line balance is to identify the ideal lot size for each product type. This is done by analyzing customer demand and determining how many units must be produced each hour to meet it.
Next, you’ll want to identify the ideal number of processes needed to produce each product type. This will help determine how many assembly lines are required so that each one can work at full capacity without being bottlenecked by another line’s slowdowns or stoppages (i.e., when there isn’t enough space on a conveyor belt).
Finally, calculate your product mix–the percentage breakdown between different products–and then determine how many units you need to produce every hour in order to meet customer demand
Step 1 – Identify the ideal lot size for each product type
The first step in balancing your production line is to identify the ideal lot size for each product type. The ideal lot size is the number of units you need to produce to meet customer demand, which depends on product type, customer demand, and product mix.
The ideal lot size represents the minimum number of products needed for a run so that there are no gaps between batches in inventory or work-in-process (WIP). If you keep producing more than this amount at any time during a process cycle–especially if those extra items are sitting around without being processed–you’ll create waste and lower overall efficiency because there will be more WIP than necessary waiting for its next operation(s) before it can move down another line or be finished up by someone else on staff who has nothing else better going on right now!
Step 2 – Identify the ideal number of processes needed to produce each product type
The next step is to identify the ideal number of processes needed to produce each product type. The ideal number of processes depends on the complexity of your products and how they’re made.
You should start by identifying all your product types, including variants (e.g., size or color). Then, you can group them into categories based on similar manufacturing methods: if all of your widgets are made with injection molding but some also require secondary machining, then these would fall into separate categories for purposes of this exercise.
Once you’ve done that, think about how many different operations are required for each category: does it require multiple steps in order for one person to complete? Or is it a single stage where someone pushes buttons until something happens? Once again, if multiple workers are involved with making each part or component–or even just one worker who performs several operations–you’ll need more than one process per category; otherwise there won’t be enough work stations available at any given time!
Step 3 – Calculate your product mix and determine how many units you need to produce every hour to meet customer demand
Once you have the V Curve, you can determine how many units of each product you need to produce every hour in order to meet customer demand. To do this, simply use a spreadsheet or other tool like Excel and add up all of your products’ demand curves. This will give you an idea of how much volume each product contributes to overall demand. Then multiply that by how many hours are left until the deadline (or whatever time period is relevant) and add them up together to get an idea of total production needed during that period of time.
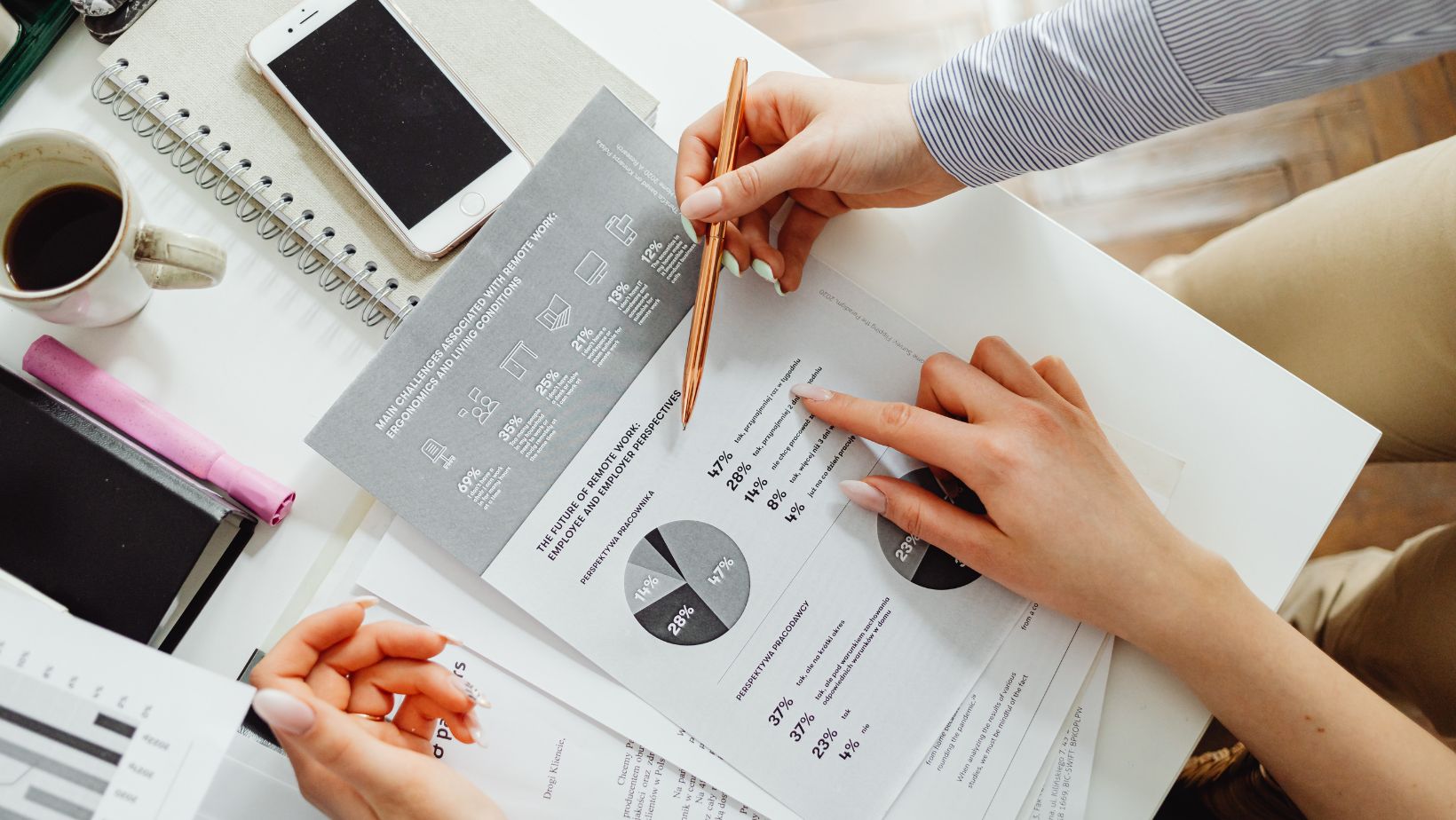
Once this has been calculated for each product group, divide the result by 2 or 3 (depending on how much variation there is between individual products). This gives us our “mastering” number–it represents how many units must be produced every hour if we want all orders completed within a given timeframe without running out of stock or having excess inventory left over at end date dueling against competitor companies vying for market share!
Step 4 – Create a simulation model for your factory layout design
In this step, you will create a simulation model for your factory layout design. A simulation model is a computer program that simulates the operation of a real-world system. It’s used for testing and evaluating different scenarios in order to understand how they affect the performance of the system as a whole, before committing resources to implement them in practice.
A production line balancing software like LineView can be used by engineers who want to optimize their production lines’ efficiency and improve throughput rates, but first they need accurate information about how their machines work together on an assembly line so that they can make informed decisions about whether certain changes would improve efficiency or not (e.g., changing where parts are placed on each station).
Conclusion
In conclusion, the V curve is a useful tool for production line balance optimization. It can help you predict how much time and money it will take to reach a certain level of productivity. However, there are many factors that affect your production line’s performance, such as equipment failure rates and worker skill levels. Therefore, it’s important not to rely solely on the V curve when making decisions about how much inventory or raw materials should be kept in stock at any given time.